3 Essential Farm Equipment Maintenance Building Construction Services In Fargo, ND
When it comes to farm equipment maintenance building construction services in Fargo, ND, there are several crucial factors to consider to ensure your facility is built to withstand the region’s harsh climate and meet your specific needs.
From choosing the right insulation materials to navigating local building codes and regulations, working with experienced professionals who understand the unique challenges of constructing farm equipment maintenance building construction services in Fargo is essential.
In this article, we’ll explore three key areas to focus on when planning your farm equipment maintenance building construction services project and provide expert insights to help you make informed decisions.
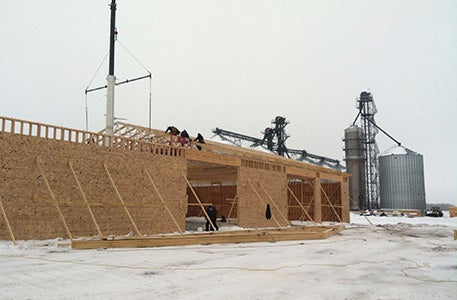
1. Choosing the Right Insulation Materials for Fargo’s Cold Winters
Proper insulation is crucial for maintaining a comfortable and energy-efficient farm equipment maintenance building in Fargo’s frigid winters.
High-performance insulation materials can help reduce heat loss, minimize energy costs, and create a more pleasant working environment for your staff.
Some of the best insulation options for Fargo’s climate include:
Insulation Material | R-Value per Inch | Benefits |
---|---|---|
Closed-Cell Spray Foam | R-6 to R-7 | High R-value, air sealing, moisture resistance |
Fiberglass Batts | R-2.2 to R-2.7 | Cost-effective, easy to install, fire-resistant |
Rigid Foam Board | R-4 to R-6.5 | Moisture-resistant, high R-value, versatile applications |
When selecting insulation materials, consider factors such as cost, performance, and ease of installation.
Working with a knowledgeable farm equipment maintenance building construction services provider can help you determine the best insulation solution for your specific needs and budget.
2. Energy Efficiency Solutions for Farm Equipment Maintenance Buildings in Fargo
Incorporating energy-efficient features into your farm equipment maintenance building can help reduce operating costs and minimize your environmental impact.
Some effective strategies to consider include:
- Installing LED lighting fixtures, which use up to 75% less energy than traditional incandescent bulbs and last significantly longer
- Investing in high-efficiency windows with low-E coatings and insulated frames to reduce heat loss and improve comfort
- Exploring solar power integration, such as photovoltaic panels or solar thermal systems, to offset energy costs and increase self-sufficiency
Energy-Saving Tip | Potential Benefits | Implementation Considerations |
---|---|---|
Programmable Thermostats | Reduces heating and cooling costs by optimizing temperature settings | Ensure compatibility with your chosen heating system |
Occupancy Sensors | Automatically turns off lights in unoccupied areas to save energy | Consider sensor placement and sensitivity settings |
Insulated Overhead Doors | Minimizes heat loss and improves energy efficiency | Choose doors with high R-values and weather sealing |
By prioritizing energy efficiency in your farm equipment maintenance building, you can create a more sustainable and cost-effective facility that benefits both your bottom line and the environment.
3. Navigating Local Building Codes and Regulations in Fargo, ND
Constructing a farm equipment maintenance building in Fargo, ND, requires adherence to various local building codes and regulations.
Some key considerations include:
- Obtaining the necessary building permits from the City of Fargo Inspections Department
- Ensuring compliance with the North Dakota State Building Code, which includes provisions for agricultural structures
- Meeting any specific zoning requirements or setback regulations for your property
- Adhering to safety codes, such as fire protection and ventilation standards, for equipment maintenance facilities
Regulatory Consideration | Potential Impact | How to Address |
---|---|---|
Building Permits | Delayed construction timeline and added costs | Submit plans early and work closely with local officials |
Zoning Requirements | Restrictions on building size, location, or use | Verify zoning compliance before starting design work |
Safety Codes | Additional design and construction requirements | Incorporate necessary features and consult with experts |
Partnering with a farm equipment maintenance building construction services provider who is well-versed in Fargo’s local building codes and regulations can help streamline the permitting and compliance process, saving you time and potential headaches down the road.
Selecting the Ideal Heating System for Your Farm Equipment Maintenance Building
Choosing the right heating system for your farm equipment maintenance building is crucial for maintaining a comfortable working environment and protecting your valuable machinery from cold-related damage.
Some popular options include:
Heating System | Pros | Cons |
---|---|---|
Radiant Heating | Even heat distribution, energy-efficient, silent operation | Higher installation costs, slower to adjust temperatures |
Forced Air Heating | Lower installation costs, quick temperature adjustments | Less even heat distribution, potential for drafts |
Infrared Heating | Targeted heating, energy-efficient, no air movement | Limited coverage area, higher equipment costs |
When selecting a heating system, consider factors such as building size, insulation levels, and the specific needs of your farm equipment.
A knowledgeable HVAC contractor or farm equipment maintenance building construction services provider can help you determine the most suitable and energy-efficient option for your facility.
Common Construction Mistakes to Avoid for Farm Equipment Maintenance Buildings in Fargo
To ensure the long-term performance and efficiency of your farm equipment maintenance building, avoid these common construction mistakes:
- Inadequate insulation or air sealing, which can lead to heat loss, energy waste, and potential moisture issues
- Poor site preparation or drainage, which can cause foundation settling, structural damage, or equipment corrosion
- Underestimating electrical or ventilation requirements, which can hinder equipment operation and create safety hazards
- Failing to plan for future expansion or equipment upgrades, which can limit your building’s long-term functionality
By working with experienced farm equipment maintenance building construction services professionals who understand the unique challenges of Fargo’s climate and agricultural needs, you can minimize the risk of these costly mistakes and ensure a successful, long-lasting facility.
Why We Think This Is Important
Investing in a well-designed and properly constructed farm equipment maintenance building is crucial for the success and efficiency of your agricultural operations in Fargo, ND.
A dedicated maintenance facility offers numerous benefits, including:
- Prolonging the life of your valuable farm equipment by providing a protected space for repairs and upkeep
- Improving worker safety and comfort by offering a climate-controlled environment for maintenance tasks
- Enhancing productivity by streamlining equipment maintenance processes and minimizing downtime
- Protecting your investment by ensuring your machinery is well-maintained and ready to perform when needed
Moreover, by prioritizing energy efficiency, compliance with local regulations, and the use of high-quality materials in your farm equipment maintenance building, you can create a facility that not only serves your immediate needs but also provides long-term value and sustainability for your agricultural operations.
By focusing on key areas such as insulation, energy efficiency, and regulatory compliance, you can ensure that your maintenance building is built to the highest standards and equipped to handle the demands of your agricultural enterprise.
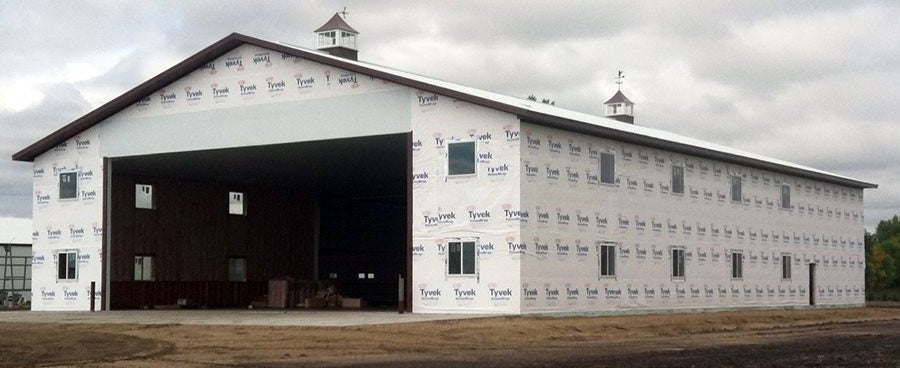
Frequently Asked Questions
What is the best insulation for a farm equipment maintenance building in Fargo’s harsh winters?
The best insulation for a farm equipment maintenance building in Fargo’s harsh winters includes closed-cell spray foam, fiberglass batts, and rigid foam board. These materials offer high R-values, moisture resistance, and air sealing properties that are essential for maintaining a comfortable and energy-efficient facility.
How can I ensure my farm equipment maintenance building is energy efficient in Fargo’s climate?
To ensure your farm equipment maintenance building is energy efficient in Fargo’s climate, consider installing LED lighting, high-efficiency windows, programmable thermostats, occupancy sensors, and insulated overhead doors. Additionally, exploring solar power integration can help offset energy costs and increase self-sufficiency.
What are the local building codes and regulations for constructing a farm equipment maintenance building in Fargo, ND?
Local building codes and regulations for constructing a farm equipment maintenance building in Fargo, ND, include obtaining necessary permits from the City of Fargo Inspections Department, complying with the North Dakota State Building Code, meeting zoning requirements and setback regulations, and adhering to safety codes for equipment maintenance facilities.
How do I select the right heating system for a farm equipment maintenance building in Fargo?
To select the right heating system for a farm equipment maintenance building in Fargo, consider factors such as building size, insulation levels, and the specific needs of your equipment. Popular options include radiant heating, forced air heating, and infrared heating. Consult with an HVAC contractor or farm equipment maintenance building construction services provider to determine the most suitable and energy-efficient option for your facility.
What are the common mistakes to avoid during farm equipment maintenance building construction in Fargo?
Common mistakes to avoid during farm equipment maintenance building construction in Fargo include inadequate insulation or air sealing, poor site preparation or drainage, underestimating electrical or ventilation requirements, and failing to plan for future expansion or equipment upgrades. Working with experienced professionals who understand Fargo’s climate and agricultural needs can help minimize these risks and ensure a successful, long-lasting facility.